Looking at today’s strip production process chain, the largest amount of CO2 is released when intensive heating processes are involved. That means CSP® plants, especially the tunnel furnace, and in strip processing, the annealing furnace. However, with CSP® Nexus and advanced annealing technology, strip production too is ready for “green steel”.
Emission-free casting and rolling with CSP® Nexus
Starting with CSP® technology. Mr. Cecere, what exactly is a CSP® Nexus plant and what makes the difference to a conventional CSP® plant?
Cosimo Cecere: “Talking about CSP® means talking about the casting and direct rolling technology. Since the invention of this technology in 1989 and the first installation at Nucor Crawfordsville, the technology stands for highly efficient steel production. We are utilizing the heat coming from the steel making plant for casting of slabs and also for the hot rolling process.
CSP® Nexus comes along with a vertical liquid bow type casting machine. Due to the bow type casting machine we have a higher throughput and we have a thicker slab. This results in much increased productivity as well as in improved quality for a one-strand plant – something that is normally related to conventional hot strip mills. Because the CSP® Nexus plant has a decoupled roughing and finishing rolling process, the roughing mill speed can be freely and very flexibly adjusted. Like in a conventional hot strip mill, the rolling speed of the roughing mill is very high in order to reduce temperature losses during the rolling process.
The high throughput of the casting machine enables also a very efficient endless mode. Endless means that in a coupled casting and rolling process we are rolling and processing the hot strip directly towards the downcoiler. The cut into coilweight is performed in front of the downcoiler. All that gives us a stable rolling of ultra-thin gauges and increased yield.”
Is it right, that the CSP® Nexus plant being part of the new H2 Green Steel complex in Sweden, is the first plant of this kind in Europe?
Cosimo Cecere: “This is correct. Worldwide, the first one is successfully operating in Texas, in the facility of SDI. So, the CSP® Nexus plant for H2 Green Steel will be the second one. Because the CSP® Nexus of H2 Green Steel comes without CO2 emissions, this will be a big advantage, compared to other plants. Looking at some “numbers”, the maximum strip width to be produced is 1,950 mm. The annual production will achieve 2.5 million tons.”
Focussing on #turningmetalsgreen, what are the features of the CSP® Nexus enabling the green transformation?
Cosimo Cecere: “The CSP® Nexus plant of H2 Green Steel will be without CO2 emissions. This is realized by replacing the tunnel furnace with a combination of electrically heated roller tables and high efficient induction heating systems supplied by SMS Elotherm. The heating function zone of the tunnel furnace will be replaced by an inductive heating solution. The state of the art induction heating by SMS Elotherm heats up the slab on a very short length and the heated roller tables to ensure the homogeneous slab temperature as well as the homogeneous transfer bar temperature. It is a hybrid solution, because it combines inductive heating with the heated roller tables.
In addition to electrical solutions like inductive heating, we offer the option to process green hydrogen, also in combination with an inductive heating unit, so that we can utilize the advantages of both solutions in one plant.”
Annealing is the key to establish carbon-neutral downstream processes
Mr. Daube, let us now look further downstream and focus on the cold strip production. How does the situation look like there in general and how could SMS group help to make a cold coil even “greener”?
Thomas Daube: “Looking from the end of the CSP® plant, the hot rolled coil is transferred to the pickling line and then the pickled coil is transported to the cold rolling mill. Mostly for any process, electricity can be used. If you are using green electricity, there is no problem to establish a carbon neutral process. In strip processing, the annealing furnace is the major source for CO2. Approximately 250 kilowatts hours per ton is needed for processing the strip in the annealing furnace. The challenge to reduce this amount of CO2 emissions.”
This is an impressive number. Can you give us some more figures to make the need even clearer?
Thomas Daube: “Sure. If you look on the carbon dioxide production, I can give some rough numbers. Not exactly, but there are about 50 kilograms per ton being emitted during the annealing process. This is a lot, indeed. The value can be reduced to four or five kilograms per ton by using electricity.”
Returning to the H2 GreenSteel project, which plants and especially which equipment do we have to consider here?
Thomas Daube: “As the coils are delivered from the CSP® Nexus plant via the pickling line and the tandem cold mill to the annealing line and further, we participate in the H2GS project with the complete process equipment, finishing with the galvanized coil. So, we cover the entire process.”
Since we mentioned already electric heaters and inductive heaters on the equipment side, is there anything to add from your side?
Thomas Daube: “Looking at the classical annealing furnace, there is always a heating zone, which may be a directly fired furnace. Moreover, there are always soaking zones with radiant tubes. This is what has to be exchanged. For the rapid heating, inductive heating has to be used. Later, the gas-fired radiant tubes have to be replaced by electrical heated radiant tubes. This is our concept, being introduced to H2GS.”
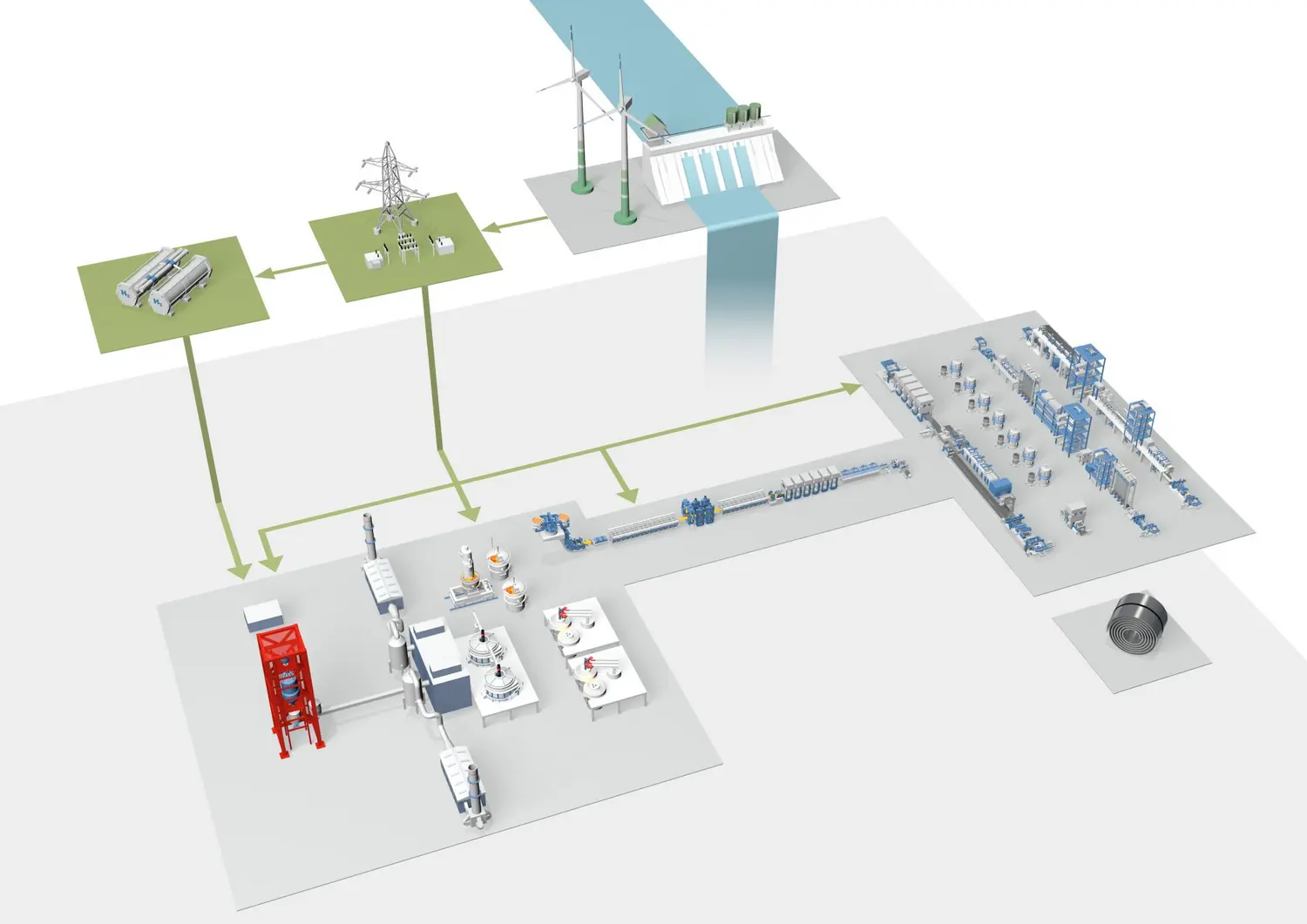
What role does digitalization play in establishing CO2-neutral flat steel production?
Thomas Daube: “Digitalization is the key to reduce the carbon footprint, because the collection of data is the basis for everything. We have the data available, so all of our lines are digital ready right now. Collecting these data, we are able to monitor the “health” of the plants. We can manage this by using a quality execution system. Quality can be managed in a way that a deviating coil is directly boxed and removed from the line. It is not processed until the very end of the process, wasting energy. The intelligent furnaces adapt the heating temperature or the annealing temperature of the strip. Considering the upstream processes, we are developing offset mini models to reduce the amount of scrap occurring during the entire production process. These are some of the digital solutions we are currently developing to reduce the carbon footprint.
Another feature is the optimal planning beforehand, meaning the manufacturing execution system, which is also the basis for everything, also to keep in mind the transition of different coils. Not to wait and to waste energy is always optimal.”
In a scale from zero to ten: How important is the topic of Green Steel for your customers?
Thomas Daube: “In my eyes it’s ten. Everybody in Europe is asking for these solutions, as we learnt in our current projects.”
Cosimo Cecere: "I can fully agree with what Thomas said. One may just go over this trade fair and may realize a plenty of “green” topics. It seems that the world turns green. And we see it really worldwide.”