Flexibility and productivity
In the entry section of strip processing lines, strips of different and partially difficult-to-weld steel grades have to be connected to form an endless strip in a short time. Old flash butt welding machines or conventional laser welding machines are not able to weld modern grades in a reliable manner, since the high alloying contents have an influence on the weld ability of the materials. Furthermore, welding machines in existing lines need to be replaced as spare parts and ‘in house expertise’ availability dwindles. Maintenance-friendly machines with high availabilities are required, which operate automatically and adaptively with desired production results.
SMS group reacted on this change process and also on the impact of digitization with this new developed welding machine. Several digital solutions are implemented to operate this machine in a simple manner. Machine features create a “today” with reduced operating and maintenance staff to perform preventive maintenance by means of long time archives recording all relevant data. The documentation of the machine is digitally available and interlinked.

Requirements
The welding machine is not only a crucial technological piece of equipment in every strip processing line, but also an entry cycle time factor and one key component for utilized and maximized production. If coils are not joined properly, the whole process will stop. Every strip break or machine stoppage has the potential to affect upstream and downstream operations resulting in significant financial implications.
The requirements to the weld seam and a reliable welding process are very high. The entire process is fully automated and the sequences to join both strip ends successfully are always the very same. What changes is the material to be welded in regards to steel quality, strip thickness, strip width and thickness from one coil to the other.
The welding process takes place every 3 to 5 minutes. In a pickling line/tandem cold mill the weld seam is bent numerous times with high tension (up to 65 tons), it travels more than 1,000 meters through the line with high speed (up to 1,200 m/min) and it eventually gets rolled and significantly reduced in thickness with high forces in five mill stands (up to 1,800 tons). Modern high-strength grades with high contents of alloying elements tend to create extreme hardness increases in the weld seam area. Induction pre- and post-heat treatment or even additional buffering wire during laser welding are mandatory for these high-tech steel grades to improve the ductility of the weld in order to allow successful production without any weld seam breakages during line run. Another major requirement of the machine is a low cycle time. Since the lines are producing continuously, the needed stops for welding have to be as short as possible.

Welding process
The process starts with ‘tail out’ threading of exiting coil and ‘head in’ threading of entering coil by means of two pinch roll units which position both ends of the coils to be laser beam welded into the welding machine. Strip centering devices located at the entry and exit side center align both strip ends. During strip centering the required welding parameters are calculated in the welder PLC based on cast analysis and strip thickness coming from level 2 data. The strip thickness is verified during clamping of both strip ends.
A double cross-cut shear is used to cut both strip ends simultaneously to prepare the strip ends for welding. The cut scrap drops through the welder’s shear onto a scrap discharge system, which is combined with the notcher scrap on a conveying belt. Test welds or notch samples can be conveyed to the operator side for inspection. In conjunction with the cutting process a hole for the weld seam detection can be punched.
The prepared strip ends are aligned relative to each other in terms of width and thickness in order to achieve the desired welding joint geometry. Before the strip ends are welded together, the position and geometry of the welding joint are measured by a camera.
In case of hard-to-weld material, the weld seam is subjected to inductive heat treatment (pre- and posttreatment) in order to obtain a homogeneous hardness profile across the weld seam.
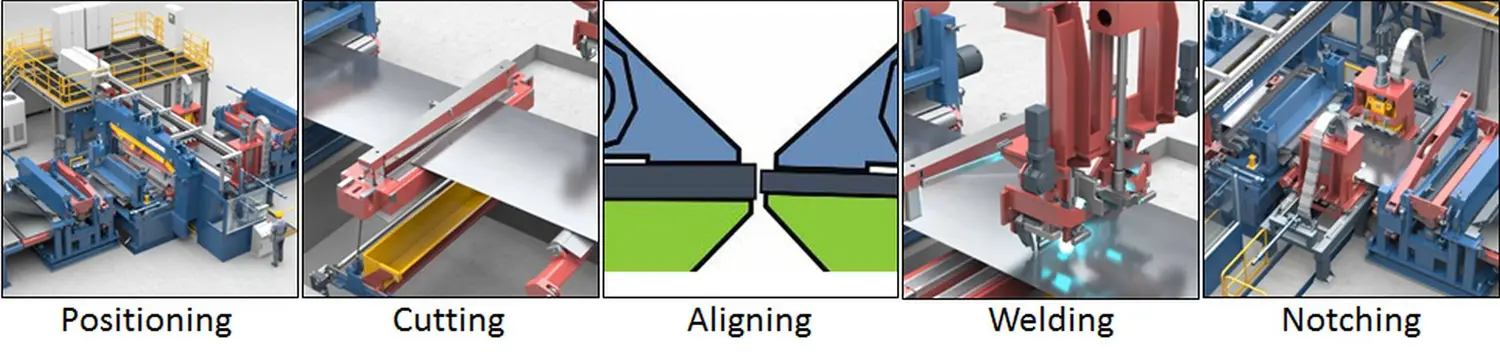
Upon completion of the welding process, the edges are removed by means of a side notcher to ensure reliable strip travel and to allow the edge trimming shear downstream in the line to move into the continuous strip. The material cut-offs can also be used for weld seam testing.
Highlights
HEAT-TREATMENT OF WELD SEAM
One major advantage of the machine is the patented inductive pre- and post-heat-treatment of the weld seam. The machine allows an individual annealing process of the hardened weld seam. Since every material combination is different and the range of possible material combinations has significantly increased, the distances between the inductive heaters and the seam as well as the power are variable. This means, the treatment time and temperature are adjusted flexibly in the most suitable way for each weld seam. The highly efficient deep heat treatment by means of medium-frequency induction allows through heating of the material in the shortest possible time, thus preventing hardness increase on the weld seam and the consequent risk of strip breakage. The special inductor design considerably reduces the holding time compared to conventional systems. This allows welding of hard-to-weld materials like martensitic or high-carbon/silicon grades.
AUTOMATIC WELD SEAM QUALITY ASSURANCE SYSTEM
The integrated automated weld-seam quality assurance system with two cameras evaluates the entire process. The first camera positions the welding head on the middle of the joint. The second camera checks and rates the quality of the welded seam. If everything is ok, the system automatically approves.
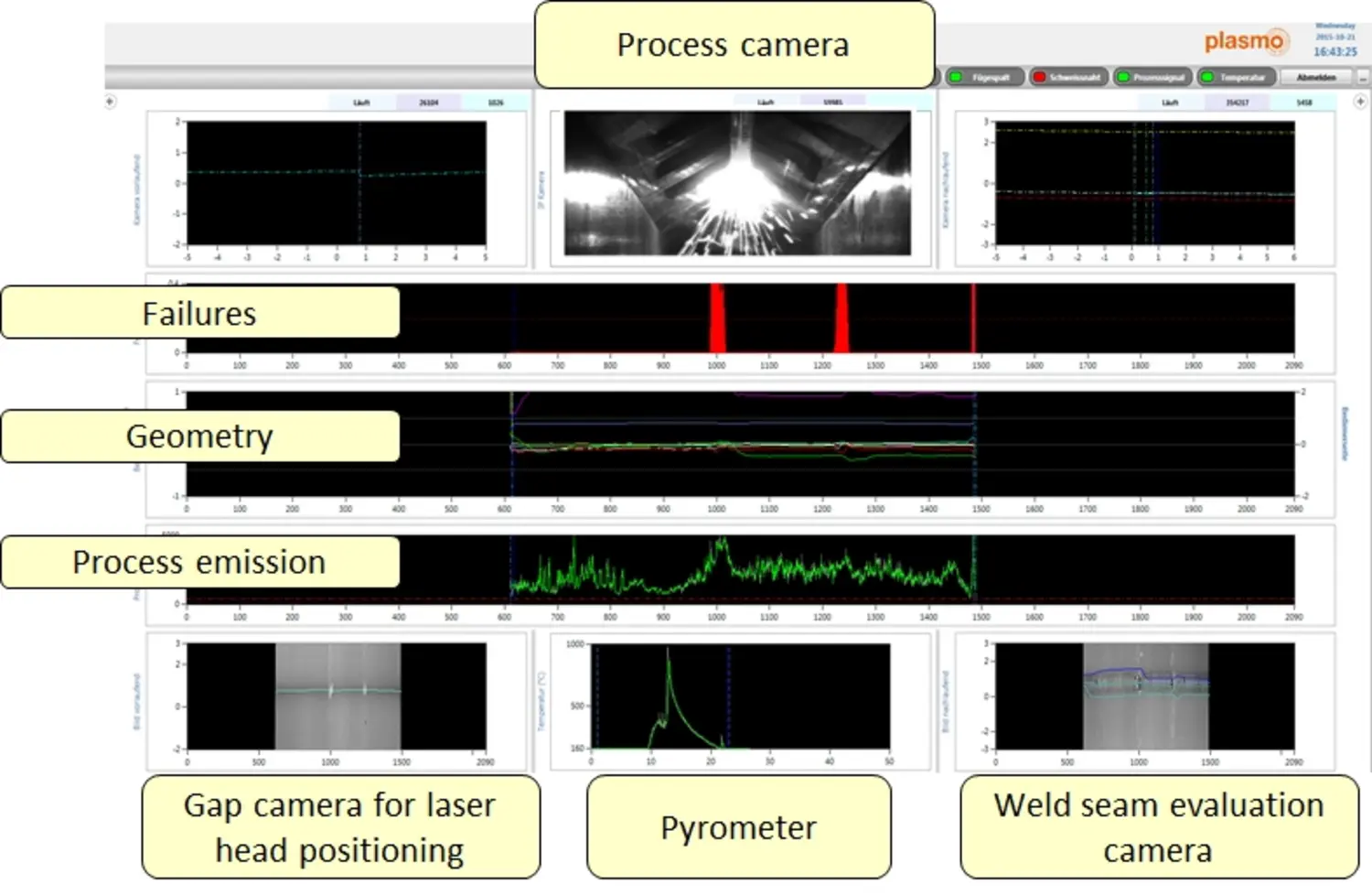
AUTOMATIC CALCULATION OF WELDING PARAMETERS
The welder is adjusted by the automatic adaptation of the welding parameters. With this system, new material pairings can be welded without extensive testing. It uses Level 2 data for cast analysis and thickness to calculate carbon equivalents and features a database with suitable welding parameters.
Thanks to the automatic calculation of the welding parameters for every individual combination of material, it is possible to weld even strip combinations of unknown steel grades. Without having to spend time on test welds and lengthy searching in databases, the correct welding parameters for the specific combination are determined immediately and reliably. All it takes for the calculation are the geometric strip data and the analysis of the steel melt of the two steel strips. Thus, test welds on the production plant or problems when welding new material combinations now are a thing of the past.
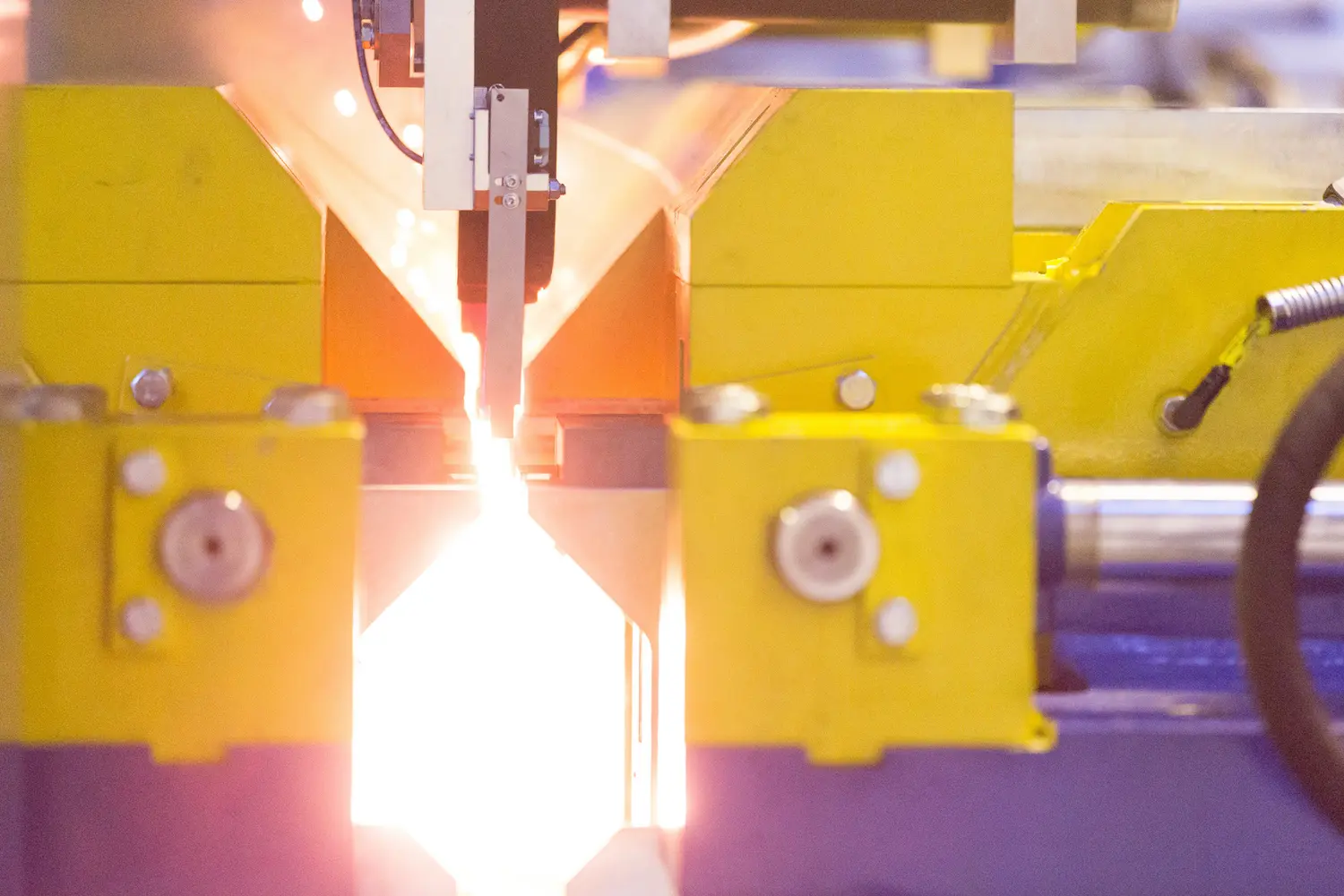
FASTEST MACHINE ON THE MARKET
Another desired feature of the machine is its cycle time of less than 60 seconds, which makes it the fastest machine on the market. Also in case of a re-weld, the time is shorter than any competitor´s solution. One reason for the short cycle time is of course the simplified design for the process. The majority of machine movements are performed linear and position controlled. Encoders for all movements allow a safe and fast positioning of the machine.
KNIVES CASSETTE CHANGING
Also the exchanging time for top and bottom knives cassettes in the shear is extremely short. They can be changed in less than 20 minutes. This is a result of a ‘smart machine design’ with no additional equipment and adjustment work needed inside the machine to allow this quick change procedure.
FREELY SELECTABLE WELDING SOURCE
Thanks to the modular design of the welding machine and the consequent separation between weld seam preparation and the welding process itself, the welding source can be easily replaced. This gives the opportunity to use a conventional carbon dioxide laser source or a state of the art solid state laser source.
The weld seam preparation with alignment, fine-cutting and joining of the two strip ends is performed by separate machine modules. Subsequently, the welding source is moved by means of a welding traversing unit along the joint between the two strip ends. In doing so, the position and traversing speed of the welding source can be adjusted individually. This fulfills an important condition for enabling other welding sources to be used in the future. Furthermore, various welding procedures can be combined. This extreme flexibility of the welding machine guarantees that for example also hybrid laser beam welding for joining stainless steel strips can be used without having to carry out major revamps.
SOLID STATE LASER
Contrary to a conventional carbon dioxide laser, the laser beam in solid state laser is generated in a resonator by means of a laser-active fiber. Thanks to its high wall plug efficiency and almost no power consumption in stand-by, operating costs will decrease by up to 90 percent.
With a solid state laser, it is possible to save or even avoid process gas (e.g. Helium) and reduce the maintenance effort. An excellent feature of the system is its simple modular structure, which is almost maintenance-free. Furthermore, solid state lasers come with a compact design and small footprint with a flexible process laser fiber enabling plant concepts to be kept simple.
The solid state laser process is rougher and more turbulent in comparison to a conventional carbon dioxide laser source by means of process stability especially on thicker grades above 3 millimeters. The appearance of spatter due to a different plasma vapor plume is well known and often described in various literature references. Certain measures were implemented to avoid these spatter appearance on gauges thicker than 3 millimeter to allow the solid state application is suitable for the strip processing process.
Modernization at SSAB Europe, Finland
The modernization of the continuous pickling line at SSAB, Hämeenlinna Works, Finland, is an example for the modernization of a line with an X-Roll® laser welder. In December 2018, the revamp project owas successfully completed with the finalization of the second phase. The comprehensive revamp included a new entry section with X-Roll® laser welder as well as a high-performance scale breaker, a horizontal looper and an extension of the pickling tank. All activities and services involved in the proj-ect, including supply of the complete electrical and automation equipment, were implement-ed by SMS group. SSAB was responsible for the civil work and overall erection.

X-Roll® laser welder at SSAB
To make sure the line will have a fast ramp-up, the X-Pact® automation system was tested and optimized in advance in a Plug & Work integration test in Germany. As all necessary equipment was available on site within a short deliv-ery period and SSAB had already finished the machine foundations, equipment installation could be started only eleven months after receipt of the order. The revamp actions had to be done within short downtimes, since the plant was expected to resume operation quickly. After the first step, the new equipment could be operated with an availability of 95 percent within six weeks. The ramp-up curve was even higher after the second step, so that four weeks later an availability of more than 98 percent could be achieved. Thus, all acceptance tests were passed within the scheduled period of time.
EXPANDED PRODUCT PORTFOLIO AND REDUCED COSTS
“SSAB modernized the pickling line to be able to process the expanded product portfolio, which includes materials with yield points of up to 900 megapascals. Modernization also enables us to reduce costs,” says Heikki Nisula, General Manager Investment Services at SSAB Europe, Hämeenlinna, Finland. “The first phase of the modernization included a completely new entry section with two payoff reels, welding machine and looper,” Christian Dornscheidt, Project Manager of SMS group, describes the scope. “We established the equipment in the open area in front of the existing pickling line during ongoing production and then connected it to the line during a one-week downtime.” The second phase was completed at the end of 2018. “The existing entry section was dismantled at the beginning of July. On new foundations in that area, a newly developed scale breaker for high-strength material was installed and the pickling line expanded by a recuperator tank,” Dornscheidt explains the comprehensive activities.
FIRST FIBER LASER IN OPERATION
In the first phase, special attention was paid to the X-Roll® laser welder which is capable of weld-ing steel strips with thicknesses between 1.5 and 6.5 millimeters and widths ranging from 650 to 1,650 millimeters to an endless strip in the entry section. The welder at the Hämeenlinna Works is the first one equipped with a solid-state laser, which means the laser beam is generated in a resonator by means of a laser-active fiber. The high efficiency combined with low maintenance costs cuts the operating expenses by up to 90 percent compared to conventional machines with carbon-dioxide laser source. Another reason for SSAB to decide in favor of an X-Roll® laser welder was the fact that the new machine permits high- alloy steel grades to be welded. “We focus on high-strength steels, and these are often very difficult to weld because of their alloy compounds,” adds Heikki Nisula and continues: “In 2015, we provided plates for welding tests at SMS group.”