Vor dem Hintergrund stetig steigender Vorgaben nach einer Verringerung des CO2-Ausstoßes und damit einhergehender Bemühungen insbesondere der Automobilindustrie hin zu leichteren Strukturen, steigt auch der Einsatz von Aluminium – und damit der Bedarf an innovativen Erwärmungsmöglichkeiten.
Vorteile der induktiven Erwärmung sind, neben dem geringen Platzbedarf, auch die flexible, dynamische Temperatureinstellung, die geringe Verzunderung oder Oxidation und neuerdings auch die Verwendung CO2-neutraler elektrischer Energie.
Durch die gute elektrische Leitfähigkeit sinkt der erzielbare elektrische Wirkungsgrad einer induktiven Erwärmung für Aluminium gegenüber der Stahlerwärmung. Nach dem Gesetz von Wiedemann-Franz geht mit einer guten elektrischen Leitfähigkeit aber auch eine gute thermische Leitfähigkeit einher. Dies bedeutet, dass Temperaturunterschiede im Material sich auch schneller ausgleichen als zum Beispiel in Stahl. Aus diesem Grund können auch Werkstücke (meist zylindrische Blöcke) aus Aluminium bis zu 800 Millimetern Durchmesser effizient und schnell induktiv erwärmt werden.
Zwei Erwärmungsverfahren
Die gängigsten Verfahren für die induktive Erwärmung von Aluminiumblöcken dsind ie Einzelerwärmung und die Durchstoßerwärmung. Bei der Einzelerwärmung sind die Blockdurchmesser eher mittel bis groß (150 bis 800 Millimeter) und die Taktzeiten lang im Bereich von wenigen bis zu 30 Minuten. Bei der Durchstoßerwärmung sind die Durchmesser klein (20 bis 150 Millimeter) und die Taktzeiten kurz (im Bereich von wenigen Sekunden).
Einzelerwärmung
Einzelerwärmung wird bevorzugt bei langen Zykluszeiten wie dem Strangpressen von Aluminiumbolzen bei großen Durchmessern gewählt. Vorteilhaft ist hier, dass flexibel unterschiedliche Blocklängen erwärmt werden können. Zudem fallen die Nebenzeiten für den Blocktransport aufgrund der langen Zykluszeiten nicht so sehr ins Gewicht. Typischerweise werden die Blöcke über ein Portal zugeführt und auf einer Transportschale vor dem Induktor abgelegt. Auf dieser Schale wird der Block ohne Reibung zwischen Werkstück und Schale in den Induktor geschoben. Hier erfolgt die Erwärmung und nachdem die benötigte Temperatur erreicht ist, wird der Block wieder an der Position vor dem Induktor für die weitere Verarbeitung zur Verfügung gestellt und über das Portal abtransportiert. Aber auch bei kleineren Durchmessern kann eine Einzelerwärmung sinnvoll sein. Hier sind beispielsweise geringe Stückzahlen in der Medizintechnik oder das Erwärmen von Aluminium bis in den thixotropen Zustand zu nennen. Der Transport kann dabei mit oder auch ohne Relativbewegung zwischen Auflage und Werkstück erfolgen.
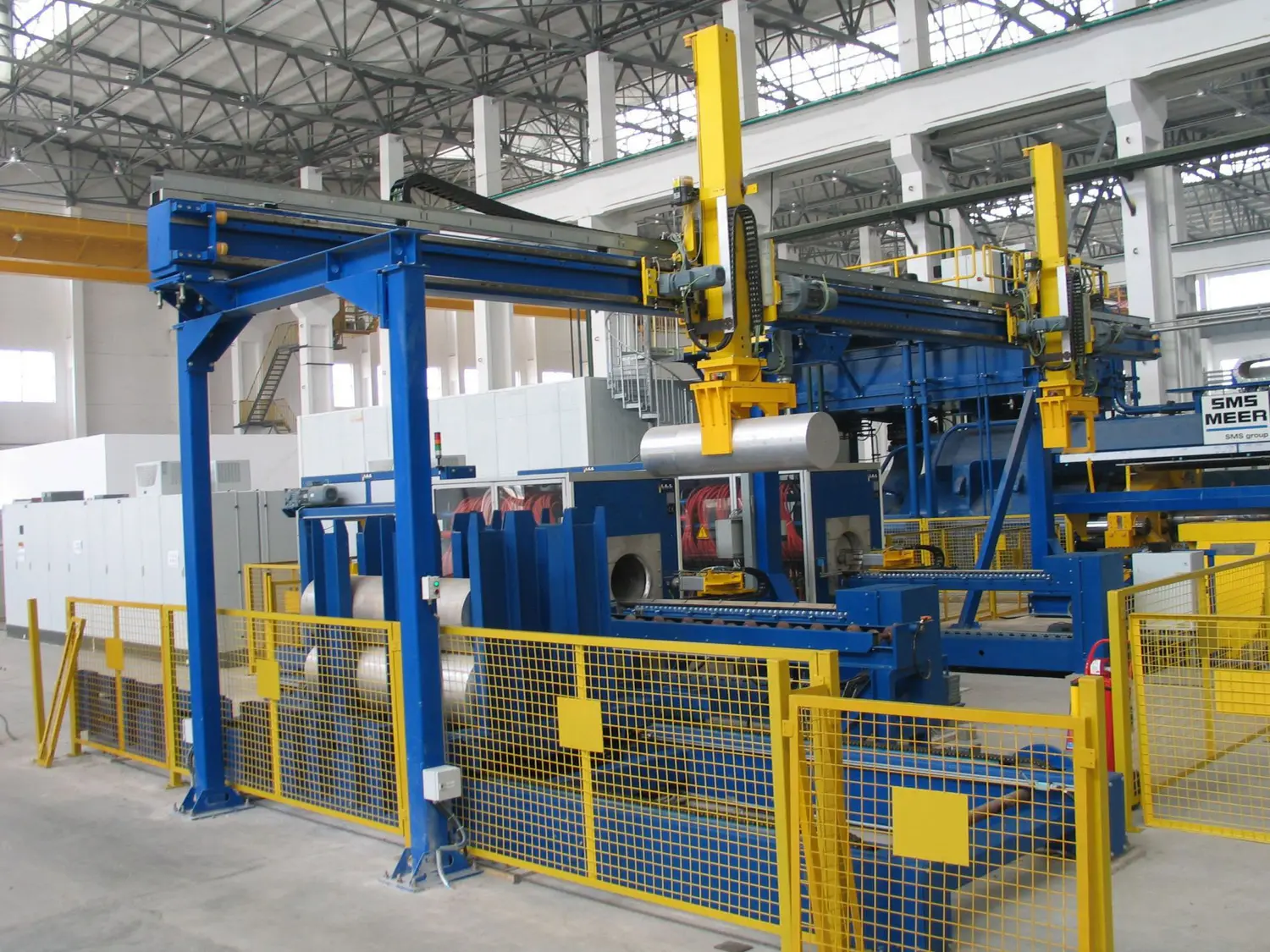
Bei der Erwärmung hat es sich besonders beim isothermen Strangpressen als vorteilhaft erwiesen, wenn die Temperatur über die Länge des Bolzens nicht absolut gleichmäßig eingestellt wird, sondern ein Anstieg über die Länge erfolgt (Taper). Aus diesem Grund sind in den dafür genutzten Induktoren unabhängig geregelte Heizzonen integriert, von der jede über eine ebenfalls separate Temperaturmessung kontrolliert wird. Dadurch kann in Stufen ein Temperaturprofil vorgewählt werden, das dann über die Leistungen in den einzelnen Zonen eingestellt und ausgeregelt wird. Durch die eingangs genannte gute thermische Leitfähigkeit von Aluminium stellt sich ein nahezu lineares Temperaturprofil über die Länge ein.
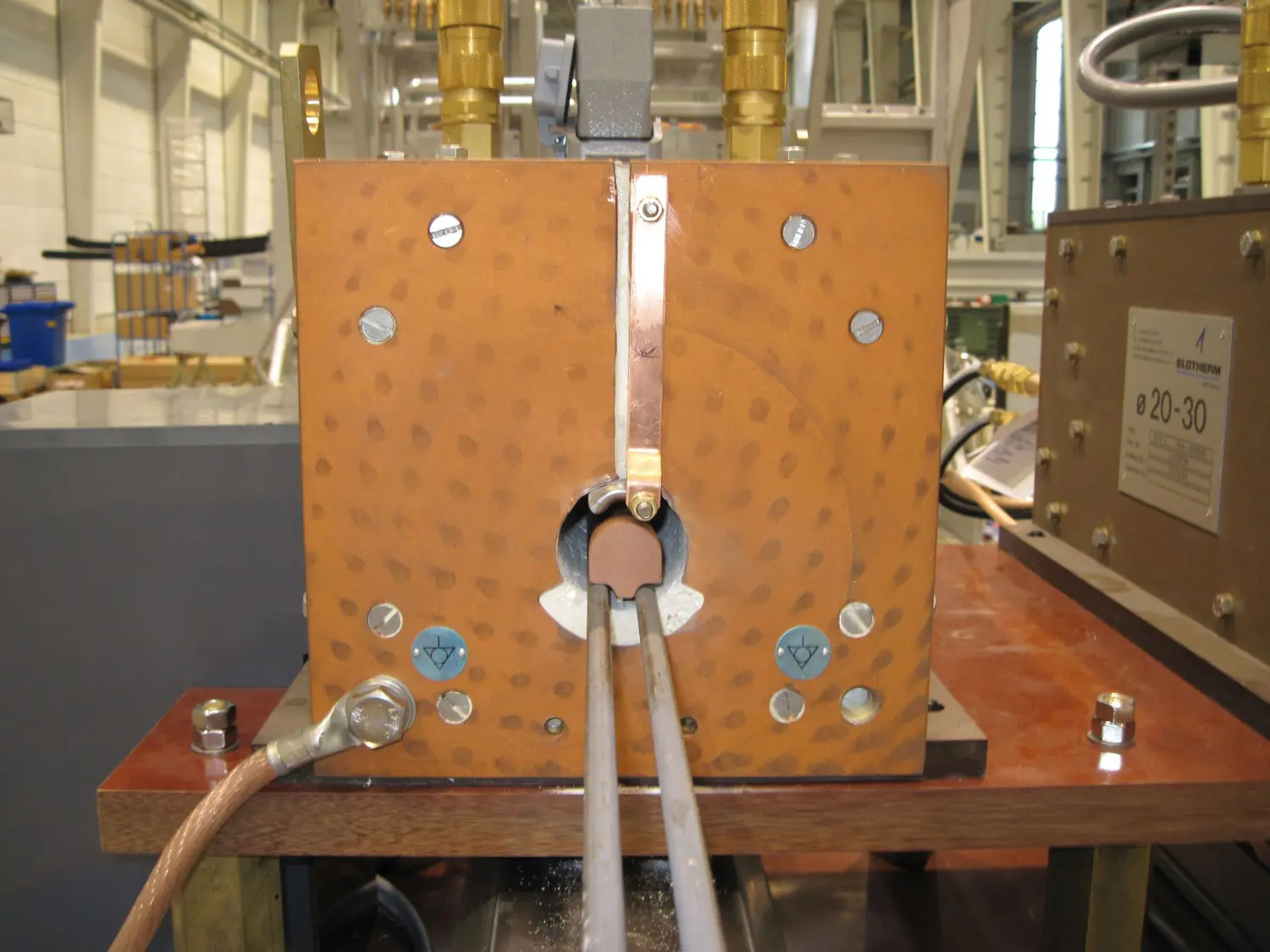
Durchstoßerwärmung
Bei der Durchstoßerwärmung erfolgt die Zuführung zur Induktionsanlage auf unterschiedliche Weise, zum Beispiel über eine Vibrationsrinne oder auch durch einen Roboter. Durch die Anlage werden die Blöcke dann hintereinander geschoben. Als Antriebsaggregat hat sich der Rollenblockdrücker bewährt, der in der Lage ist, die Materialsäule sowohl kontinuierlich als auch getaktet zu bewegen. Die Säule liegt während der Erwärmung auf wassergekühlten Materialführungsrohren und gleitet auch auf diesen.
Bandtransport
Da bei kleinen Abmessungen (< 60 Millimeter) die Stückgewichte gering sind, gibt es bezogen auf die Oberflächenqualität bei der Durchstoßerwärmung kaum Probleme durch Riefenbildung. Ab einer kritischen Kombination aus Stückgewicht und geforderter Oberflächenqualität kann es aber sein, dass die Materialführungsrohre im Heißbereich die Oberfläche zu sehr beeinflussen. Gleichzeitig ist aber in diesem Durchmesserbereich auch die Taktzeit noch nicht lang genug für eine Einzelerwärmung bzw. der Aufwand dafür unverhältnismäßig hoch.
An dieser Stelle soll der Bandtransport anknüpfen. Er verbindet die Vorteile der oben genannten Erwärmungsarten und kann bei mittleren Durchmessern, auch kurze Taktzeiten ohne Relativbewegung zwischen Werkstück und Maschine realisieren. Dabei wird anstelle einer Transportschale ein endlos umlaufendes Band aus Textilgewebe genutzt, auf dem die Werkstücke aufliegen.
Eine Herausforderung wird hier an das Bandmaterial gestellt. Es darf nicht elektrisch leitfähig sein und muss Temperaturen von ca. 500 Grad Celsius dauerhaft aushalten. Als Transportkonzept wurde eine Kombination aus Ziehen und Schieben gewählt, um die mechanische Belastung des Bandes möglichst gering zu halten und damit eine hohe Lebensdauer des Bandes zu erzielen. Der weiter oben bereits erwähnte Rollenblockdrücker wird synchron zu einem Bandantrieb gefahren, der ein Aufschieben des Bandes verhindert und nur unterstützend arbeiten muss. Das Band wird durch den Induktorsatz zurück zum Induktoreinlauf transportiert und über Umlenkrollen in den Induktorsatz ein- und ausgefädelt. Ein auf diesem Band liegender Bolzen wird somit durch den Rollenblockdrücker geschoben, während gleichzeitig das Band durch den Antrieb synchron gezogen wird. Das Ergebnis ist ein vollständig ohne Relativbewegung an der Oberfläche des Werkstücks realisierter Materialtransport. Die Oberflächenqualität entspricht dem Ausgangszustand.
Hybridanlage
Sollte der Bedarf für eine reine Aluminiumproduktion nicht ausreichend für die Auslastung einer Pressenlinie sein, ist unter Umständen eine Wechselmöglichkeit von Vorteil. Das hybride Konzept sieht den Betrieb eines konventionellen Induktorsatzes für Stahl vor und bietet gleichzeitig die Möglichkeit, nur durch Umrüsten des Induktorsatzes auch Aluminium mit einem Bandtransport zu erwärmen. Durch die thermophysikalischen Eigenschaften von Aluminium und die geringere Schmiedetemperatur können beide Induktorsätze mit dem gleichen maximalen Durchsatz betrieben werden. Somit kann die installierte Umrichterleistung optimal bei beiden Produkten genutzt werden.
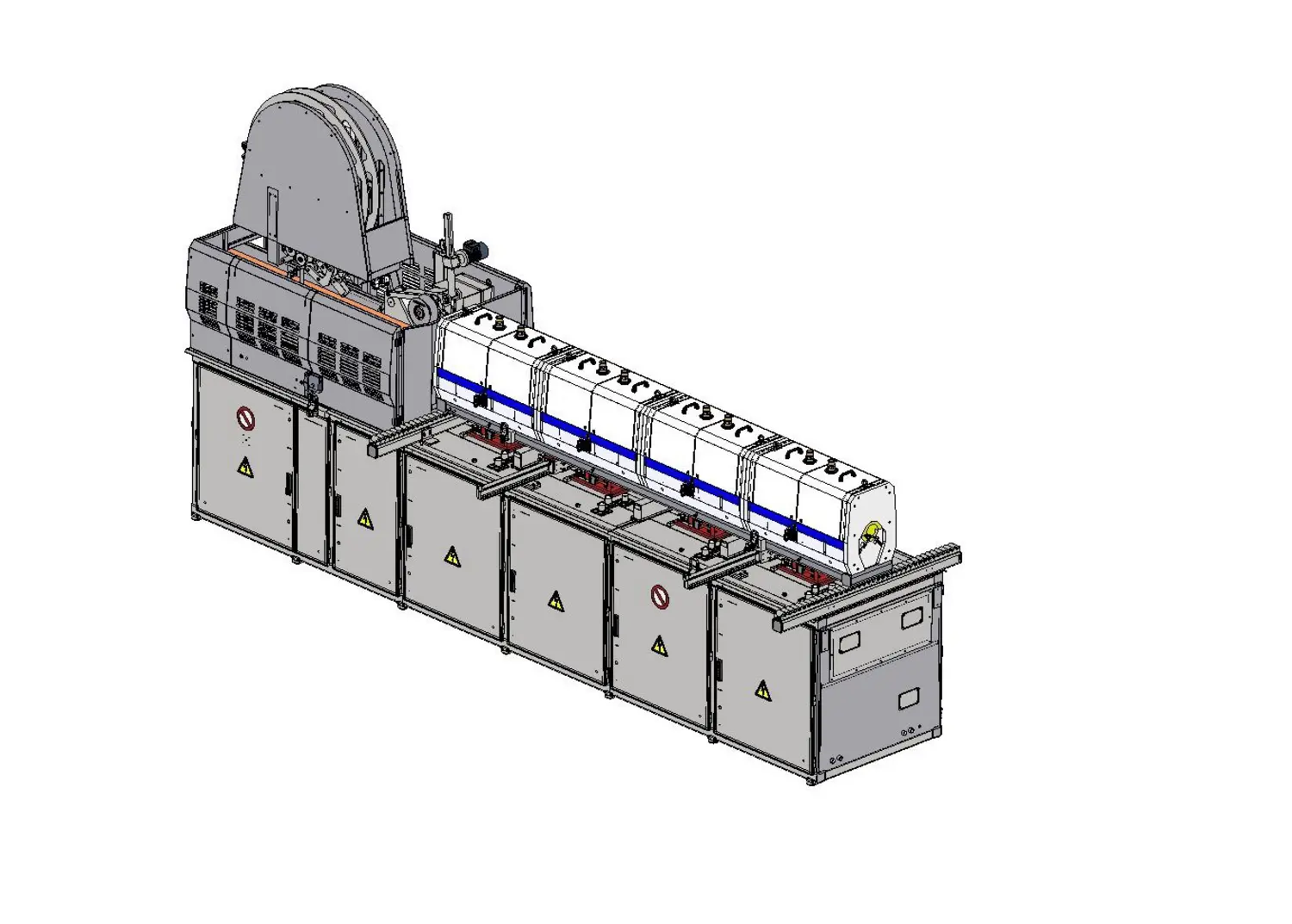
Weiterführende Information
Mehr Informationen zum Thema Induktion, zur Anlagentechnik und Referenzen finden Sie auf www.sms-elotherm.com.